A BLDC motor (brushless DC motor) is a rotating motor with permanent magnets in the rotor and windings that are part of the stator. The brushless DC motor replaces the mechanical commutator on the brushed DC motor with an electric commutator, which is powered by a DC power supply through an integrated inverter/switching power supply to generate AC electrical signals to drive the motor. BLDC motors have high efficiency and good operability, widely used in various transmission industries, and are expected to bring low power consumption.
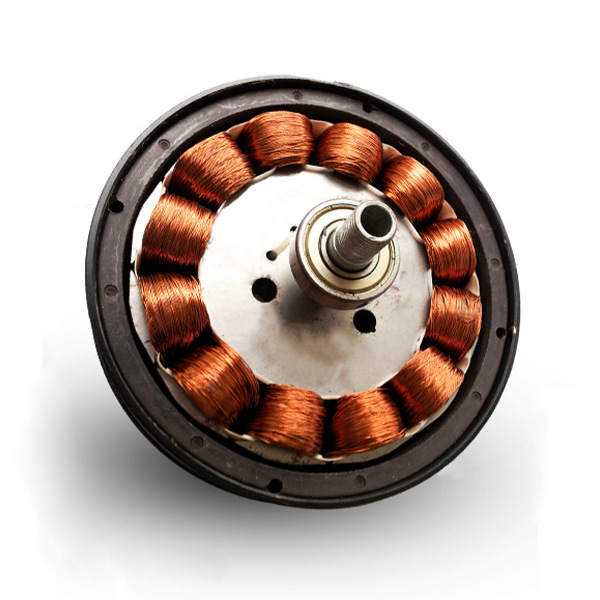
DC motor (brushed motor)
Placing a coil in a magnetic field, through the flow of current, the coil will be repelled by one side of the magnetic pole and attracted by the other side of the magnetic pole, continuously rotating under this action. During the rotation process, the current flowing in the opposite direction to the coil continues to rotate. The commutator part of the motor is powered by electric brushes, which are located above the commutator and move continuously with rotation. By changing the position of the brush, the direction of the current can be changed, and the commutator and brush are essential structures for the rotation of DC motors.
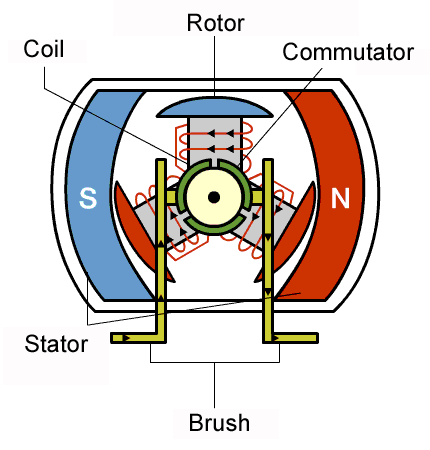
BLDC motor
The term ‘BrushLess’ in BLDC motors means’ brushless’, which means that the brushes in DC motors (brushed motors) are gone. The role of electric brushes in DC motors (brushed motors) is to energize the coils inside the rotor through a commutator. BLDC motors use permanent magnets as the rotor, which does not have coils inside. As there are no coils inside the rotor, there is no need for commutators or brushes for electrification. Instead, coils are used as the stator.
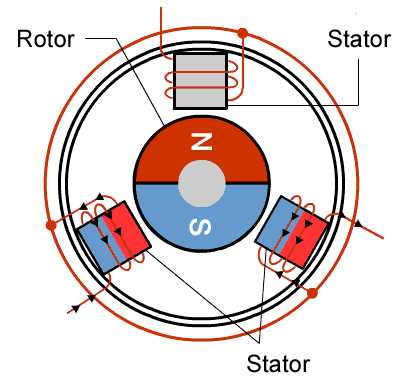
The magnetic field produced by the fixed permanent magnet of a DC motor (brushed motor) does not move. It rotates by controlling the magnetic field generated by the coil (rotor) and changes the number of rotations by changing the voltage. The rotor of a BLDC motor is a permanent magnet that rotates by changing the direction of the magnetic field generated by the surrounding coils. The rotation of the rotor is controlled by controlling the direction and magnitude of the current flowing to the coils.
Advantages of BLDC motors
There are three or more coils on the stator of a BLDC motor, each coil has two wires, and the motor has at least six lead wires in total. In fact, due to the internal wiring, only three wires are usually required, but it is still one more wire than the previously mentioned DC motor (brushed motor), and it will not move by connecting the positive and negative poles of the battery.
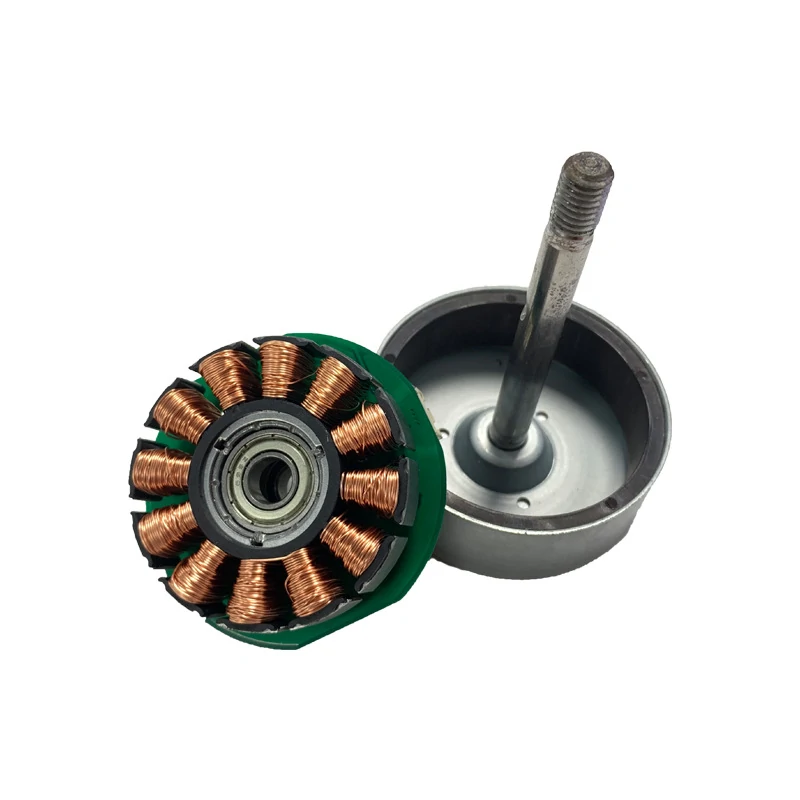
High efficiency, can control the rotational force (torque) to always maintain the maximum value. During the rotation process of DC motors (brushed motors), the maximum torque can only be maintained for a moment and cannot always maintain the maximum value. If a DC motor (brushed motor) wants to achieve the same torque as a BLDC motor, it can only increase its magnet, which is why even small BLDC motors can emit strong force.
With good controllability, BLDC motors can achieve the desired torque, rotation number, etc. without any deviation. BLDC motors can accurately feedback the target rotation number, torque, etc. Through precise control, the heating and power consumption of the motor can be suppressed. If it is battery driven, the driving time can be extended through careful control.
Durable, with low electrical noise, DC motors (brushed motors) will experience wear and tear over time due to the contact between the brush and commutator. The contact area will also generate sparks, especially when the gap between the commutator touches the brush, which will produce huge sparks and noise. If you do not want to generate noise during use, you will consider using a BLDC motor.
The purpose of BLDC motor
Where are efficient, versatile, and long-lasting BLDC motors typically used? Often used in products that can demonstrate their high efficiency and long lifespan, and are continuously used. For example, household appliances have recently started using BLDC motors in electric fans, which have successfully reduced power consumption significantly due to their high efficiency. By changing the control system, a significant increase in the number of rotations has been achieved. The vacuum cleaner demonstrates the excellent controllability of the BLDC motor. As an important storage medium, the hard disk also uses BLDC motors for its rotating parts. As it is a motor that requires long-term operation, durability is crucial. It also has the purpose of strongly suppressing electricity consumption, and high efficiency is related to low electricity consumption.
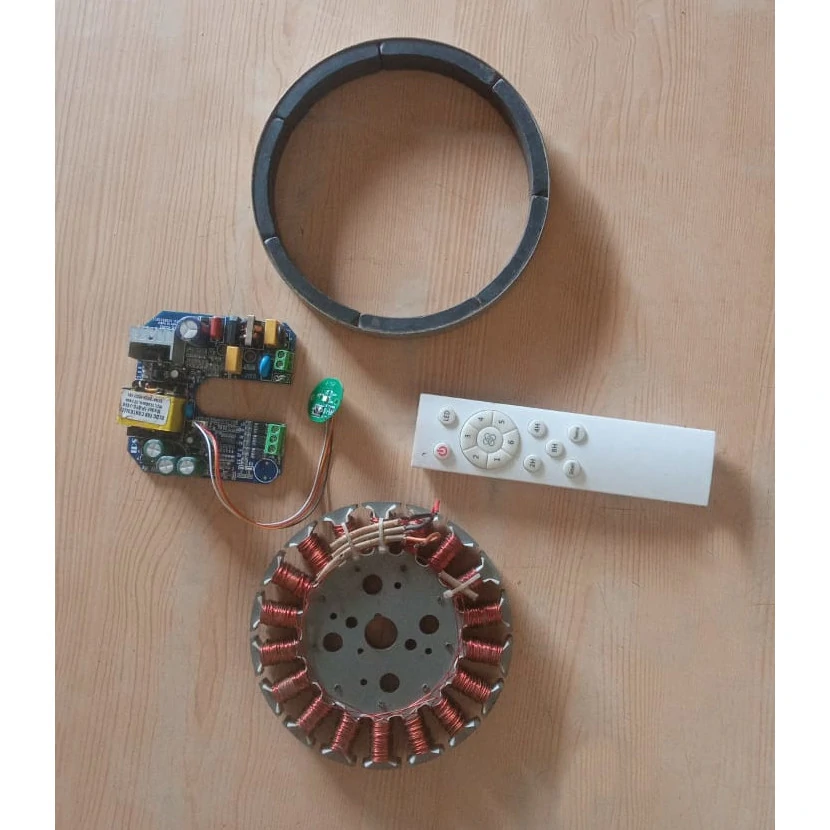
Conclusion
Brushless motors have many advantages over brushed DC motors, including high torque to weight ratio, greater torque (higher efficiency), higher reliability, lower noise, longer lifespan (brushless and commutator corrosion), elimination of ionizing sparks generated by commutators, and comprehensive reduction of electromagnetic interference. Due to the fact that the winding is supported by the casing, it can be cooled through conduction without the need for internal airflow in the motor. This, in turn, means that the interior of the motor can be completely enclosed to prevent dust or other foreign objects from entering.
BLDC motors will be more suitable for force control in small robots. If stepper motors are used, structures like robot wrists need to be fixed in a certain position and provide a considerable amount of current. BLDC motors can cooperate with external forces to provide only the required power, thereby suppressing power consumption. BLDC motors are also suitable for unmanned aerial vehicles, especially those with multi axis frames. As they control the flight attitude by changing the rotation of the propeller, BLDC motors that can precisely control the rotation have advantages.
Leave a Reply